21 May 2023
At a recent event for investors, Tesla presented an idea that may change the way cars are made around the world.
The manufacturing idea is called the unboxed process.
If it succeeds in reducing the cost of electric cars, analysts say the process might change the way all automakers build cars.
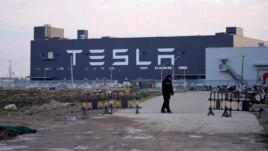
FILE - A Tesla sign is seen on the Shanghai Gigafactory of the U.S. electric car maker before a delivery ceremony in Shanghai, China January 7, 2020. (REUTERS/Aly Song/File Photo)
To understand Tesla's idea, it is important to know that most automakers now use a system first designed by the Japanese company, Toyota.
Toyota's process is the Toyota Production System. The carmaker first builds the body of the car and then moves it along an assembly line. Workers and robots put parts of the car, such as the engine and seats, into the "box" of the car as it moves. After the outside metal panels are added, the car is painted.
But Tesla says it wants to change the way cars are made.
Tesla thinks it can reduce costs by making large pieces separately and putting them together at the last moment. In the "unboxed" system, parts of the car such as the outside metal, doors, and front end are painted separately and then joined together at the end. Some parts of the car will be first connected to a large battery pack and then added to the overall structure.
Tesla said in a statement that it wants to "build more vehicles at a lower cost." The aim is to cut the final cost of an electric car from over $40,000 to under $30,000.
The assembly system will not be used until at least late 2024, when a manufacturing center opens in Monterrey, Mexico. Tesla is building the center for a cost of $5 billion.
Martin French is a director at Berylls, an automotive research company. He studies the industry's move to electric vehicles. French said Tesla's idea is a direct challenge to Toyota.
He said, "I got the feeling when I watched the Tesla (presentation) that the Toyota Production System handbook has just been thrown up in the air and machine-gunned down."
Jan-Philipp Buchler is a researcher at the Free University of Dortmund in Germany. Buchler said the Tesla process will increase production speed and reduce complexity. He called the idea "revolutionary."
However, critics note that some Tesla ideas have failed to work in real life. They point to problems with the company's self-driving systems and the Cybertruck, which has been delayed for some time.
In addition, production experts say the Tesla plan does not consider all parts of the process in the same way as the Toyota system.
James Womack of the Massachusetts Institute of Technology wrote a book about Toyota's production methods. He said the main difference is that Toyota's plan was a system that helped automakers run their entire business. While Tesla's idea is only "an assembly process."
Hide Oba is a Japanese manufacturing expert who once worked for Toyota. Oba warned that Tesla's plan will only work if the "unboxed vehicle modules are completely synchronized, and finished blocks arrive for a final put-together just-in-time."
He also wondered if Tesla will be able to use the unboxed system for different vehicle models in the same production center. He said he thinks it is "next to impossible" because making large parts of the car separately may not permit manufacturing changes, like when the company designs a new model.
He said that limitation "could become a drag on the company's overall efficiency."
I'm Dan Friedell.
Dan Friedell adapted this story for Learning English based on a report by Reuters.
__________________________________________________________________
Words in This Story
assembly line –n. a line of machines, equipment, workers, etc., in a factory that builds a product by passing work from one station to the next until the product is finished
panel –n. a piece of metal that makes up part of a car's exterior
challenge –v. to test the ability of something or someone to stay in their current position; in this case a company
handbook –n. a book or document that gives information about how to do something
gunned-down –v. shot down in a dramatic way
module–n. a piece of something larger, such as a section of a car
synchronized –adj. something that fits together just right
efficiency –n. the ability to do something without extra effort or extremely hard work